Untangling the Mystery of Porosity in Welding: Tips for Reducing Flaws and Making The Most Of Quality
In the detailed world of welding, porosity continues to be a relentless challenge that can significantly impact the high quality and stability of welded joints. As we dive right into the depths of porosity in welding, uncovering the keys to its avoidance and control will be paramount for specialists looking for to master the art of high-quality weldments.
Recognizing Porosity in Welding
Porosity in welding, a typical issue encountered by welders, describes the presence of gas pockets or gaps in the welded material, which can jeopardize the integrity and top quality of the weld. These gas pockets are normally trapped throughout the welding process as a result of different factors such as incorrect shielding gas, polluted base products, or inaccurate welding criteria. The formation of porosity can damage the weld, making it prone to cracking and rust, inevitably resulting in architectural failures.
Recognizing the source of porosity is critical for welders to efficiently stop its occurrence. By acknowledging the value of maintaining appropriate gas securing, guaranteeing the tidiness of base products, and optimizing welding settings, welders can substantially lower the possibility of porosity formation. In addition, making use of methods like pre-heating the base product, employing appropriate welding methods, and performing thorough evaluations post-welding can additionally assist in minimizing porosity problems. Generally, a detailed understanding of porosity in welding is crucial for welders to produce top quality and sturdy welds.
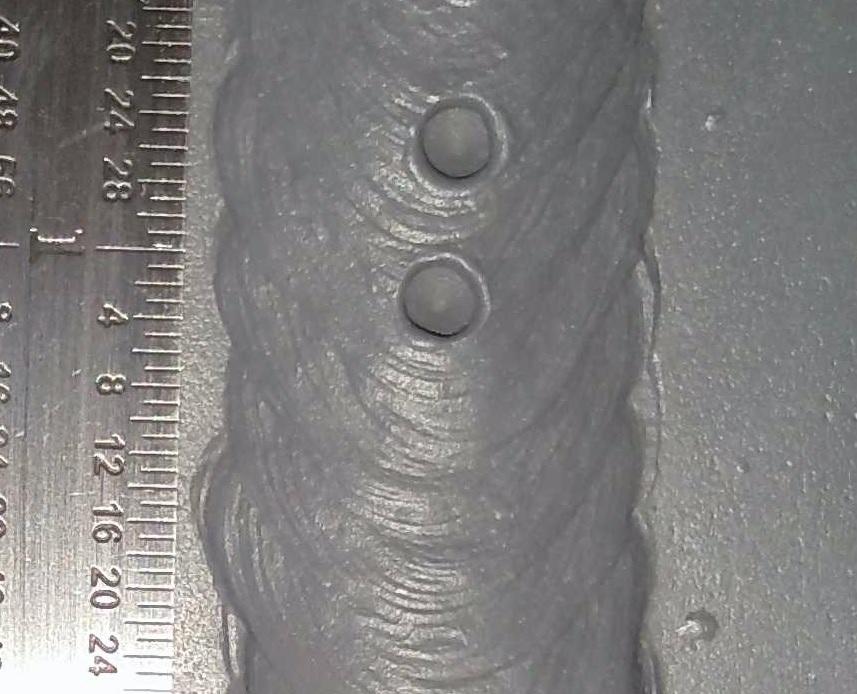
Usual Sources Of Porosity
When evaluating welding procedures for prospective high quality issues, recognizing the typical reasons for porosity is essential for keeping weld stability and avoiding structural failings. Porosity, characterized by the visibility of tooth cavities or gaps in the weld metal, can significantly jeopardize the mechanical residential properties of a welded joint. One typical reason for porosity is inappropriate shielding gas insurance coverage. Inadequate securing gas flow rates or inappropriate gas mixes can bring about atmospheric contamination, causing porosity formation.
Another common root cause of porosity is the visibility of dampness and contaminants on the surface of the base metal or filler material. When welding products are not effectively cleansed or are exposed to high levels of humidity, the vaporization of these pollutants throughout welding can develop gaps within the weld grain. In addition, welding at improper criteria, such as exceedingly high traveling rates or currents, can create excessive disturbance in the weld swimming pool, capturing gases and creating porosity. By attending to these usual reasons with appropriate gas protecting, product preparation, and adherence to ideal welding parameters, welders can minimize porosity and enhance the quality of their welds.
Methods for Porosity Prevention
Applying reliable precautionary steps is essential in minimizing the like it event of porosity in welding processes. One strategy for porosity prevention is ensuring appropriate cleaning of the base metal before welding. Pollutants such as oil, grease, corrosion, and paint can cause porosity, so extensive cleaning making use of suitable solvents or mechanical approaches is vital.

Another trick precautionary measure is the choice of the right welding consumables. Using premium filler products and protecting gases that appropriate for the base metal and welding procedure can significantly reduce the danger of porosity. Additionally, preserving proper welding specifications, such as voltage, current, travel speed, and gas flow rate, is essential for porosity prevention. Deviating from the advised setups can result in incorrect gas insurance coverage and inadequate combination, leading to porosity.
In addition, using correct welding techniques, such as maintaining a consistent travel speed, electrode angle, and arc length, can help avoid porosity (What is Porosity). Appropriate training of welders to guarantee they comply with finest methods and high quality control treatments is likewise vital in lessening porosity issues in welding
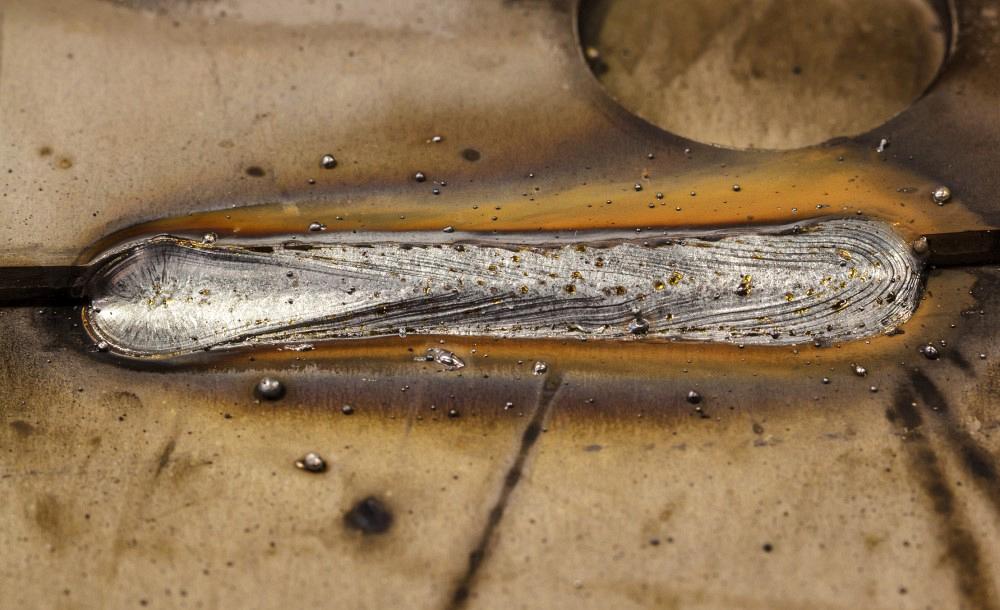
Finest Practices for Quality Welds
One trick method is keeping appropriate cleanliness in the welding area. Extensively cleaning up the work surface and surrounding area prior to welding can help mitigate these concerns.
An additional ideal technique is to meticulously pick the ideal welding criteria for the specific products being signed up with. Correct specification choice makes certain ideal weld infiltration, combination, and overall top quality. Making use of high-grade welding consumables, such as electrodes and filler steels, can substantially affect the final weld top quality.
Relevance of Porosity Control
Porosity control plays a crucial duty in making sure the stability and quality of welding joints. Porosity, identified by the existence of cavities or gaps within the read weld steel, can considerably endanger the mechanical properties and architectural integrity of the weld. Too much porosity compromises the weld, making it a lot more susceptible to fracturing, rust, and total failure under functional tons.
Effective porosity control is necessary for maintaining the preferred mechanical buildings, such as strength, ductility, and durability, of the bonded joint. What is Porosity. By minimizing porosity, welders can enhance the general top quality and integrity of the weld, ensuring that it satisfies the efficiency needs of the desired application
Furthermore, porosity control is vital for find accomplishing the preferred visual look of the weld. Too much porosity not just damages the weld but also interferes with its visual appeal, which can be vital in markets where looks are important. Proper porosity control techniques, such as using the correct shielding gas, regulating the welding criteria, and making certain correct sanitation of the base products, are necessary for creating top notch welds with very little problems.
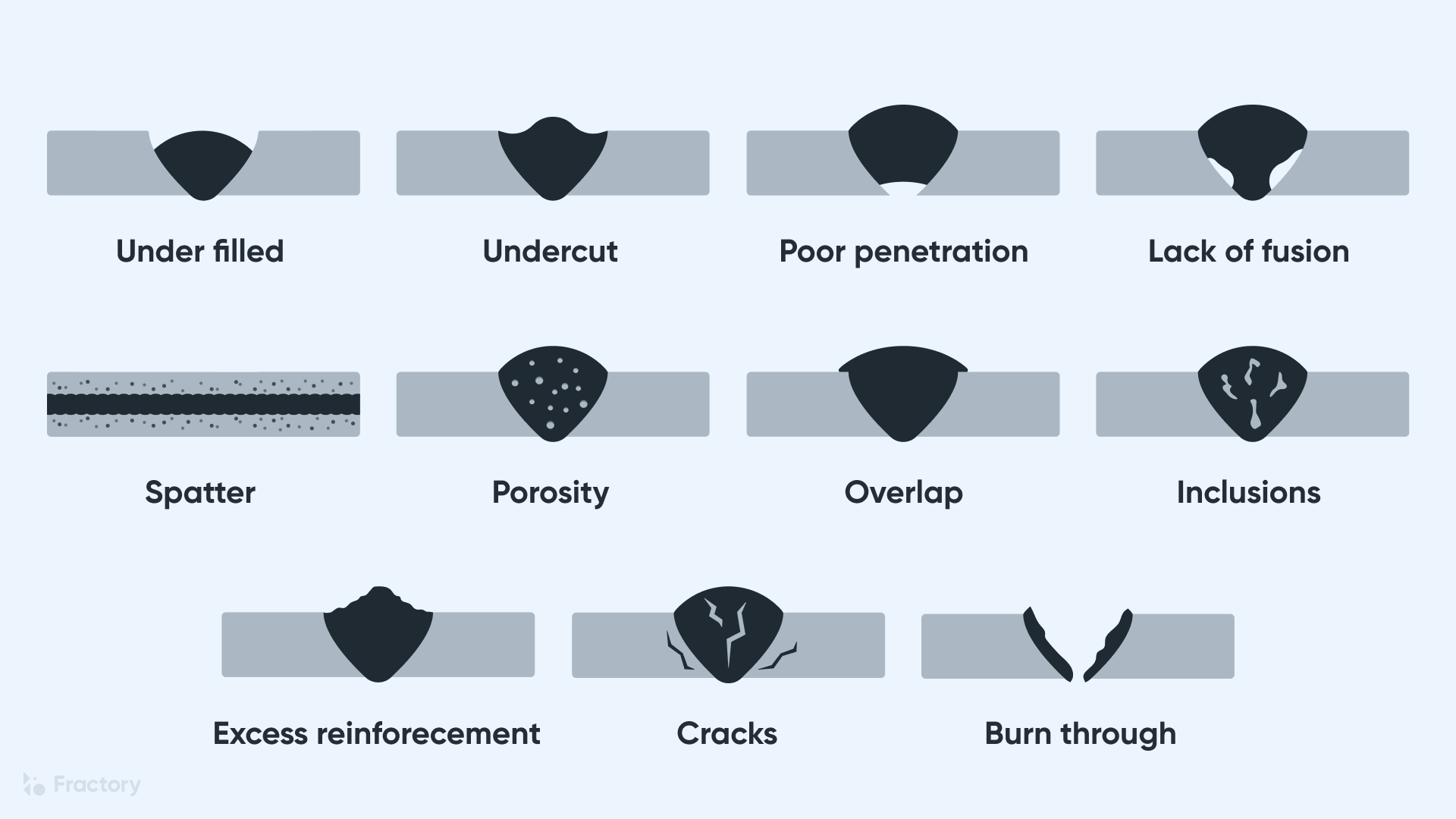
Verdict
To conclude, porosity in welding is a typical problem that can compromise the top quality of the weld. By comprehending the root causes of porosity and applying appropriate avoidance techniques, welders can minimize flaws and accomplish better welds. It is vital to control porosity in welding to make certain the stability and toughness of the last product. Applying finest techniques for porosity control is vital for achieving optimum welding results.